Slot die coating is slowly but steadily becoming a norm in coating depositions. It surely is becoming a platform technology for many applications. Slot die coatings serve industries including, but not limited to, Li-ion battery, multi-layer ceramic displays, solar cells, OLED, LCD displays, pharmaceutical and food packaging.
Slot die coating is effective in providing precise thin coatings with good accuracy. It is a pre-metered coating technique as opposed to the conventional coatings like knife-on-roll or reverse roll methods.
In a pre-metered coating, the amount of fluid applied to the web per unit area is pre-determined by a fluid metering device upstream. In this way, the average cross-web weight (thickness) is pre-determined before the fluid is applied to the substrate.
To elaborate on pre-metering, this means that the thickness of the final coating is a function of the rate at which the fluid comes in contact with the substrate. In this pre-metered coating, the wet film coating thickness can be easily calculated from the pump rate (the rate at which fluid enters the system), the substrate motion speed (the rate at which the substrate absorbs fluid from the system), and the coating width (the width across which the fluid is distributed on the substrate).
The advantages of pre-metered coatings are:
- The wet thickness can be easily pre-judged within operating range of process
- Wet thickness does not depend on formulation changes
- Even multi-component reactive systems can be coated
- Multiple layers can be coated simultaneously
- Excellent coating uniformity both in the cross-web or machine direction
In the self-metered technique, the final wet thickness of the coated web is controlled by the interactions of the fluid flow with the coating applicator.
The slot die process enables good control over fluid usage and deposition. This allows for a huge waste reduction in terms of complete and effective use of the fluid to be coated – leading to cost reduction.
Slot die coating beats all the existing fluid coating/deposition techniques when comes to achieving the thinnest coating possible. The advantageous feature however is that, it would also enable the deposition of thick coatings. Slot process could render coatings/films of thickness ranging from tens of nanometers to hundreds of microns. On top of that, slot die method enables deposition from a wide range of fluids and chemistries (from nanodispersions to particle slurries and suspensions) enabling a wide window of materials coating deposition capabilities.
The key components of a slot die head unit are:
- Two thick exterior plates
- Carefully designed screws (number of screws and alignment) to keep the plates tight with desired width and to align the die in perfect uniformity.
- A manifold in one of the plates to guide the fluid. This is a specially designed hollow cavity to hold the fluid distributed evenly (dead volume) before entering the coating substrate.
- An ultrathin metal/plastic plate called shim. This shim can be designed to suit coating deposition. For example, the shim shape can be designed to render striped/patterned coatings.
- A meniscus-guide. This is to guide the fluid uniformly onto the substrate to improve coating quality and stability.
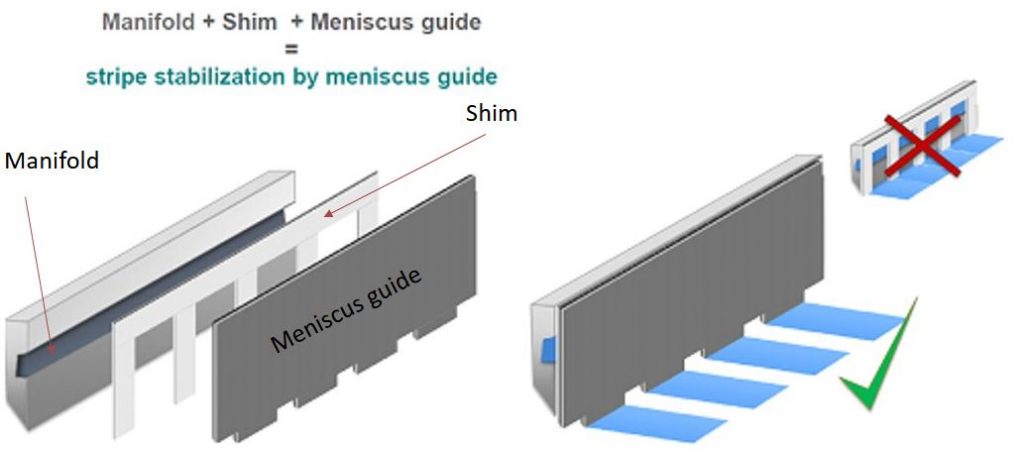
Figure: Schematic drawing of the components of a slot die head unit. Image courtesy: Coatema®
The simple head unit design of slot dies greatly simplifies the assembly, disassembly, and cleaning of the parts.
In the laboratory range slot dies, the dead volume of the slot-die coating heads can be designed to process even very low volumes of fluids (hundreds of microliters to a few milliliters).
They can be operated with a single shim or with a shim kit comprising shim and meniscus-guide for producing stripe/pattern coatings at low web speeds (0.1 – 5 m/min).
Slot dies can be your go-to laboratory or industry level tool, if you are looking to render ultrathin to thick coatings with precise control over cross-web thickness and uniformity. They also work well under low pressure with low viscosity fluids/inks.
Slot dies can be integrated to existing industry-scale coatings with less difficulty – positive R&D project and commercial outcomes. The scalability of slot die processes from R & D to mass production is less complex.
The interior design of a slot die head is critical to its effectiveness. In a typical slot die coating process, the coating fluid is pumped into the head via tubing by a continuous and controlled forward displacement mechanism. The tubing would be connected to the slot die head through an inlet located at the front or back plate. Upon entering the slot die head, the fluid evenly fills/distributes in the specially designed (according to desired end-product) manifold. The fluid is then guided on to the coating edge – lip – of the slot die head by the shim. The thickness and design/pattern of the shim determines the coating width and stripe pattern of the fluid, applied on the substrate.
Depending on the requirement/end use, slot dies can be manufactured into a variety of geometries and designs. Some are:
- Fixed lip
- Adjustable lip
- Flexible lip and roll
- Curved lip
- Fixed lip with shim
- Fixed lip with shim and meniscus-guide
- Single layer coating die
- Multilayer coating die
Components of a complete slot die coating machinery
Apart from the slot die unit, a lab level or a pilot plant slot die coating machinery must include these components:
- Slot die positioner: This is to allow the slot die to be placed in relation to the substrate with precise control. Slot die can be placed hanging over the substrate, horizontally in contact with the substrate, not in contact with the substrate with precise substrate-to-die gap, and in a tensioned web over slot die (TWOSD) design, all depending on the desired end coating product.
- The drying unit/chamber. It is also critical for the finished product to be dried under optimum drying conditions. These conditions depend on factors such as the solvents used, the coating thickness and the interfacial chemistry between the substrate and the coating material. The speed of the coating process, the temperature used for drying and the solvent extraction procedures in place are all important factors that define the end-product.
- A series of idler rollers and unwinding and rewinding units with precise forward and backward motion and tension control.
Critical process parameters of slot die coating are:
- Rheology of coating fluids
- Substrate condition / chemistry
- Fluid delivery / pumping speed and consistency
- Fluid deposition speed / volume
- Operation speed
- Web tension control
- Edge control
- Resolution and process accuracy of coating / laminating systems
- Precision of coating operations
- Curing / drying (hot air with extraction)
Briefly, precise and repeatable deposition of ultrathin to thick films can be achieved by carefully designing the slot die, its positioner, the web conveyor mechanisms, fluid delivery system and the drying unit.
Key highlights of slot die heads
- Have only a few parts / components
- Available in a selection of materials to suit different applications / requirements (composite, alloy, stainless steel and silicon carbide)
- Simple assembly, disassembly features
- Easy to clean and maintain
- Fits to all coating and printing platforms
- Can render both continuous and striped / patterned coatings
- Very low dead volume to render well-defined thin coating
- Option to provide wide range of coating widths (narrow to wide)
- Carefully designed shims and meniscus guides to fit applications
The ever-increasing demands of manufacturing thin films and coatings with precise control over their chemistry, uniformity and thickness is putting slot die as the preferred coating technique across a wide range of application fields and industries. The consistency and uniformity of the coatings rendered by slot dies, and their scalability have resulted in a good number of lab-scale projects. The market share of slot die technology in the coating industry is also increasing steadily with more industries willing to upgrade their existing coating technologies to slot die technology.
Relevant industries:
Batteries and capacitors: Lithium-ion battery electrodes, multilayer ceramic capacitors, OTFT Batteries, photoreceptor Cells
Micro-electronics: Flat panel displays, thin circuits, LCD and OLED display components, sensors
Barrier films: Food and medical packages – to deposit thin food-grade coatings. O₂ barriers, OTR (oxygen transmission rate), WVTR (water vapor transmission rate), paper, film and foil, textiles and adhesives.
Solar photovoltaic: Thin organic / inorganic coatings with controlled chemistry is the key.
Medical diagnostics: Controlled and accurate deposition of therapeutics or diagnostic drugs. Variations in chemistries and thickness can result in variations in performance. Medical/Surgical products and packaging.
Transdermal and oral pharmaceuticals: Strictly defined coatings will deliver controlled and accurate dosage. IVD test strips, membranes, oxygen barriers.
Slot die background
Slot Die coating was originally developed in the early 1950s, and in 1951 Eastman Kodak Co. filed the first patent principles for Slot Die coating.
Process flow ideas
- Unwinder
- Idler roller-controlled web flow. Tension control.
- Pre-treatment (corona/plasma)
- Slot die head with positioner
- Drying
- Laminator
- Rewinder
Advantages of slot die coating technology
- Higher cost-efficiency resulting in a good Return on Investment (ROI)
- Less material consumption due to high precision pre-metered coating
- Less material wastage / high efficiency and less solvent contamination issues
- Uniformity of coating over the entire web width (±5 % or better)
- Low maintenance (no wear parts)
- Wide range of viscosity with the same die
- Can achieve a wide range of thicknesses: from 20 nm to > 200 μm
- Able to coat organic or inorganic liquids / slurries on flexible or rigid substrates
- Slot die heads available from R&D sizes to large width ranges up to 2000 mm
- Scalable from R&D to pilot scale and mass production with less process complexity
Disadvantages of slot-die coating technology
- Defects due to instabilities in the coating bead meniscus where the coating process exits the stable coating window. Or what could be classed as external factors either relating to the delivery of fluid, movement of the substrate, or the viscoelastic properties of the solution.
- Sensitive technology with respect to solution viscoelastic properties, rheology and other external factors such as the delivery of fluid and the movement of substrate.
Required safety measures and certifications
ATEX and CE certification. Lower Explosive Limit (LEL) certified system.
Slot die coating thickness
The average wet thickness can be easily calculated from the specific flow rate, q (cm3/s/cm width) and the web speed U (m/min)
i.e. Hwet = q/U
It is not affected by any other parameters.
Manifold
Manifold in a slot die head influences the distribution of fluid across the head width. Manifold design is optimized to maintain a constant flow rate across the width of the slot-die head, which works independent of the solution viscosity and flow rates.
The stability of the wet film coating is defined by the width (b) of slot die head and its channel length (L). The channel comprises the slot and land of the head unit, mainly the length from the manifold to the lip. These two together controls the drop in pressure of the fluid within the slot die head (D; delp), which defines the stability of the coating. The flow of fluid through this channel is represented by the Pouiselle Flow equation:
The drop in pressure, D, is determined by the flow rate (V) and viscosity (m) of the solution, and the channel length (L) and channel width (b) of the slot die head.
Dp = 12mLV/b3
The equation shows that the major factor that controls the pressure drop is the slot die/channel width. Once a slot die head is designed and manufactured, the pressure drop can further be manipulated using shims of various thickness, size and shape. i.e. by using shims of different sizes for different flow rates or solution viscosities, the pressure drop can be maintained at a fixed value.
If you are looking to buy / build your own slot die coater, please fill in the form below. We might be able to get suitable quotes for you.